NTN Corporation (hereinafter referred to as NTN) has developed “insulated coated bearings” for tri-electric systems (e-Axle) for pure electric (EV) and hybrid (HEV) vehicles that are resistant to galvanic corrosion.
To prevent the passage of electric current inside the bearing, NTN has coated the outer diameter and end surfaces of the bearing with an insulating film that can withstand voltages of 100V or more, providing excellent insulating characteristics and responding to the market trend towards higher voltages in new energy vehicles.
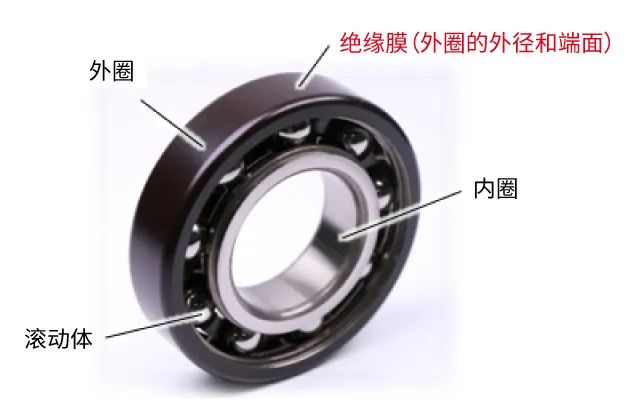
Electrolysis-resistant bearings for e-Axle (bearings with insulating coating)
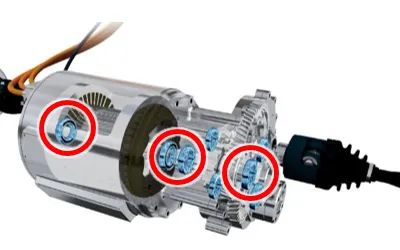
Example of application in parallel axis e-Axle (circled in red)
R&D Background
In recent years, various industries have been promoting decarbonisation and emission reduction, so the automotive market is also accelerating the development and popularisation of environmentally friendly models, led by EVs and HEVs. These vehicles, which are mainly powered by electric motors, are equipped with a triple electric system (e-Axle) that combines an electric motor, an inverter and a gearbox.
The e-Axle is electrically driven, but the electric current passing through the bearings generates electrical sparks that cause corrosion and spalling of the metal tissue, so overcoming the electrical corrosion caused by leakage is a problem for bearings in triple-electric systems.
Advantages of R&D products
Electrical corrosion resistance | By applying an insulating coating to the outer diameter and end faces of the bearing outer ring, the current passing through the bearing is reduced, making it insulated to withstand voltages of 100V or more. The bearings for electric motors can withstand voltages of less than 10% of the battery voltage, so they will be able to withstand future increases in battery voltage to 800V. |
Heat dissipation | Because the thickness of the coating combines electrical corrosion resistance and heat dissipation, it has the same heat dissipation as the uncoated standard product. |
Wear resistance | The insulating film has a low coefficient of friction and good wear resistance, reducing the total wear on the outer diameter of the outer ring and the inner wall of the bearing housing by 88% compared to the uncoated standard. The thickness of the coating required for insulation can be maintained even in the event of creep and slippage of the fixed outer ring. |
<Outer track surface after galvanic corrosion test>
The standard will produce the corrugated sheet-like damage characteristic of galvanic corrosion.
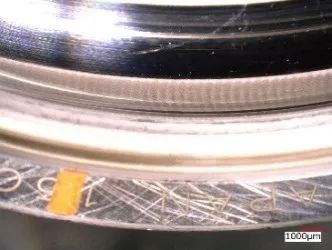
Standard products
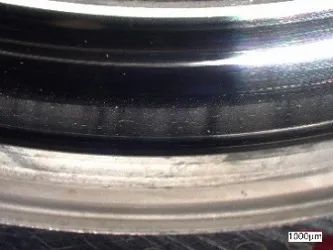
R&D Products
In addition, the insulation coating developed here can be applied to all types of NTN bearings on the e-Axle, including NTN’s high-speed deep groove ball bearings.
Note
Galvanic corrosion of the e-Axle
In order to increase the range of new energy vehicles and shorten the battery charging time, the voltage of EV batteries is becoming higher and higher. It is expected that 800V batteries will become popular in the future, but the effect of galvanic corrosion on bearings due to high voltage will also become greater.
In addition, the control frequency of inverters is increasing in order to control motors more efficiently, and it is expected that the number of electrical sparks will increase, leading to a higher chance of galvanic corrosion.
NTN’s products for the e-Axle
In order to extend the range of the vehicle and save electricity, the e-Axle is moving towards a smaller and lighter size. In addition to small size and light weight, the motor needs to have high torque and high power to meet the driving requirements, which requires bearings with high speed.
On the other hand, as the e-Axle becomes lighter, the bearing and bearing housing become thinner and thinner, and the outer ring of the bearing is susceptible to run-out slippage under the additional load. This leads to wear and tear of the bearing, which in turn leads to eccentricity and tilting of the bearing, resulting in noise and vibration in the housing, and the resulting grinding powder reduces the life of the bearing.
In this context, NTN has developed and supplied a product that is suitable for high speed rotation and bearing outer ring creep slippage to suit the e-Axle operating environment.
*The “insulated coated bearing” is not yet available.