In the future, NTN will continue to conduct experiments to verify the feasibility of this technology in order to realise its practical application and provide quality after-sales services.
- SEPTEMBER 15, 2023
The use of AI for proper maintenance of machines and equipments
Contribute to increased productivity
NTN Corporation (hereinafter referred to as NTN) has developed a new technology to detect bearing life with high accuracy by combining multiple AIs. This technology can more accurately predict the service life of bearings from the occurrence of spalling to complete damage. The development of this technology will help improve the efficiency of maintenance planning for machinery and equipment, which in turn will lead to cost savings and increased productivity.
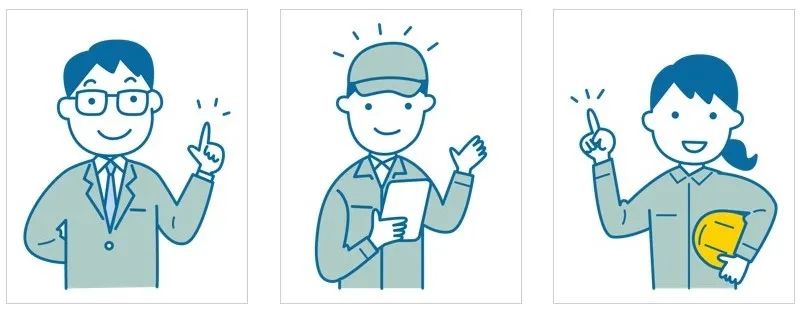
During long-term use, bearings in machinery and equipment may become slightly spalled. If this spalling occurs in areas that are not easily accessible for maintenance, the machine may continue to operate without affecting normal operation. Although the condition of the bearings can be known through vibration data testing, it is difficult to accurately predict how long a bearing will last after spalling has occurred. Often, the choice is either to replace the bearing as soon as possible or to wait until the bearing is completely damaged. In addition, some skilled tradesmen can judge when to replace a bearing based on years of experience. However, with the development of labour saving and automation, in order to reduce machine and equipment downtime and lower maintenance costs, there is a growing need for high precision life inspection technology to more accurately detect when a bearing should be replaced.
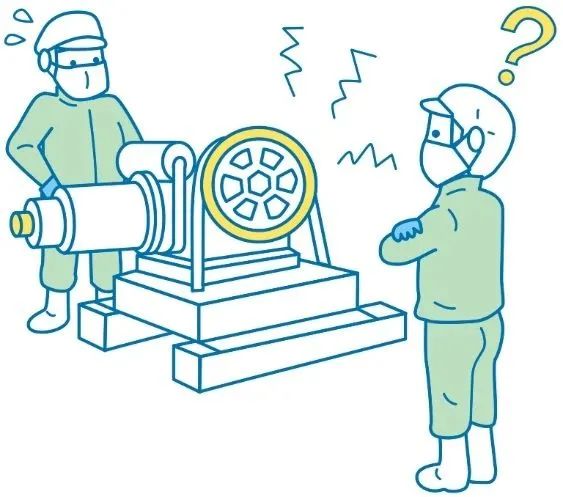
NTN’s recently developed life inspection technology combines deep learning and Bayesian learning to predict with high accuracy the life of a bearing from the occurrence of spalling to breakage. Among a number of AI models, NTN chose a convolutional neural network that specialises in image processing, which enables the detection of the damage state and life span of bearings by converting the vibration data of bearings into image data. In addition, NTN used Bayesian linear regression to create a more reliable prediction model, taking into account individual differences in bearing damage and errors in the detection data. Taken together, NTN’s new technology improves inspection accuracy by 30% compared to conventional methods (compared to NTN’s conventional inspection methods).
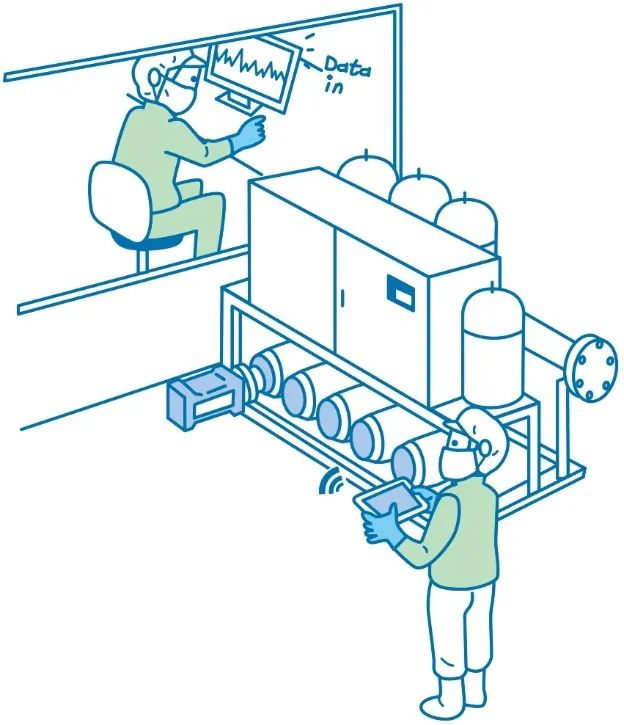
NTN and the Graduate School of Engineering at Osaka University established the NTN Next Generation Collaborative Research Institute in 2017. Under the umbrella of the Institute, NTN and the research team of Associate Professor Kenichi Fukui (Graduate School of Industrial Science) at Osaka University have been engaged in intensive collaboration and joint research and development. This innovative technology was successfully realised by combining NTN’s extensive experience in bearing technology with Osaka University’s achievements in advanced AI research.
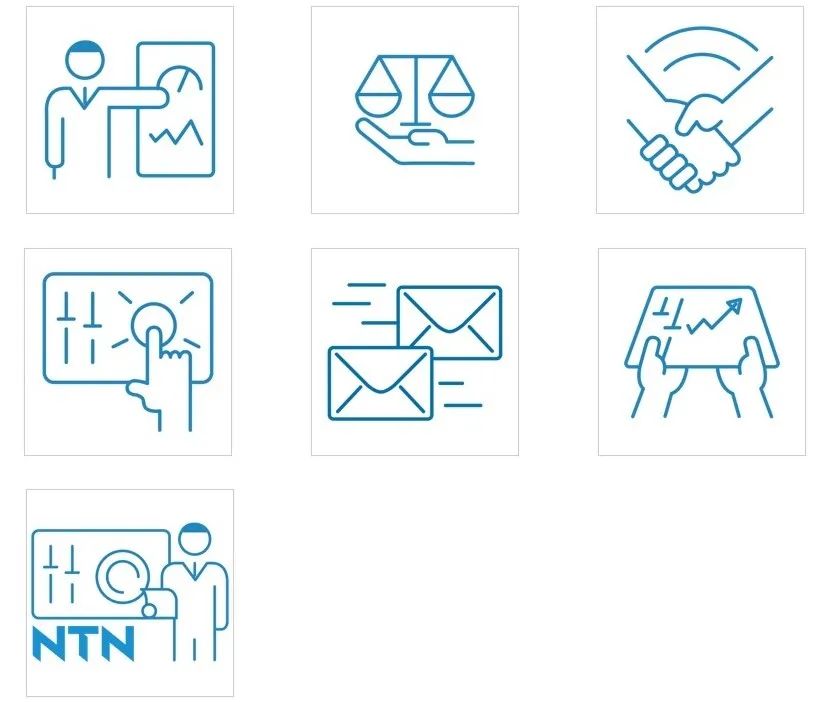
NTN
NTN is working to apply this technology to practical maintenance services to keep bearings in optimal condition by repairing machinery and equipment in a timely manner, thereby improving productivity and reducing environmental impact.
In the future, NTN will continue to conduct experiments to verify the feasibility of this technology in order to realise its practical application and provide quality after-sales services.